Facility Design and Factory Layout
Make the most of your facility design project. Partner with Campbell Corporation’s facility layout and planning experts to develop designs and specifications that’ll help you meet your customers’ demand while improving revenue.
Contact Us
Thinking of Relocating?
Forge your company’s future with a world-class facility
Experienced manufacturers know that a facility layout design project is the perfect opportunity to increase revenue, reduce lead times, and improve efficiency through application of Lean techniques. Campbell Corporation brings decades of Lean manufacturing facility planning experience to the table when partnering with you to design a new factory or facility layout. Our recommendations are practical, based on your goals and capabilities, and focused on your success. Rather than applying a cookie-cutter approach to manufacturing cycle efficiency, we tailor our methods and the tools we bring to bear so that you are able to seize opportunities for your business.
Let’s talk about how we can help you meet your manufacturing goals with a new facility, redesigned layout, or expanded operation. Want to know how we do it? Read on.
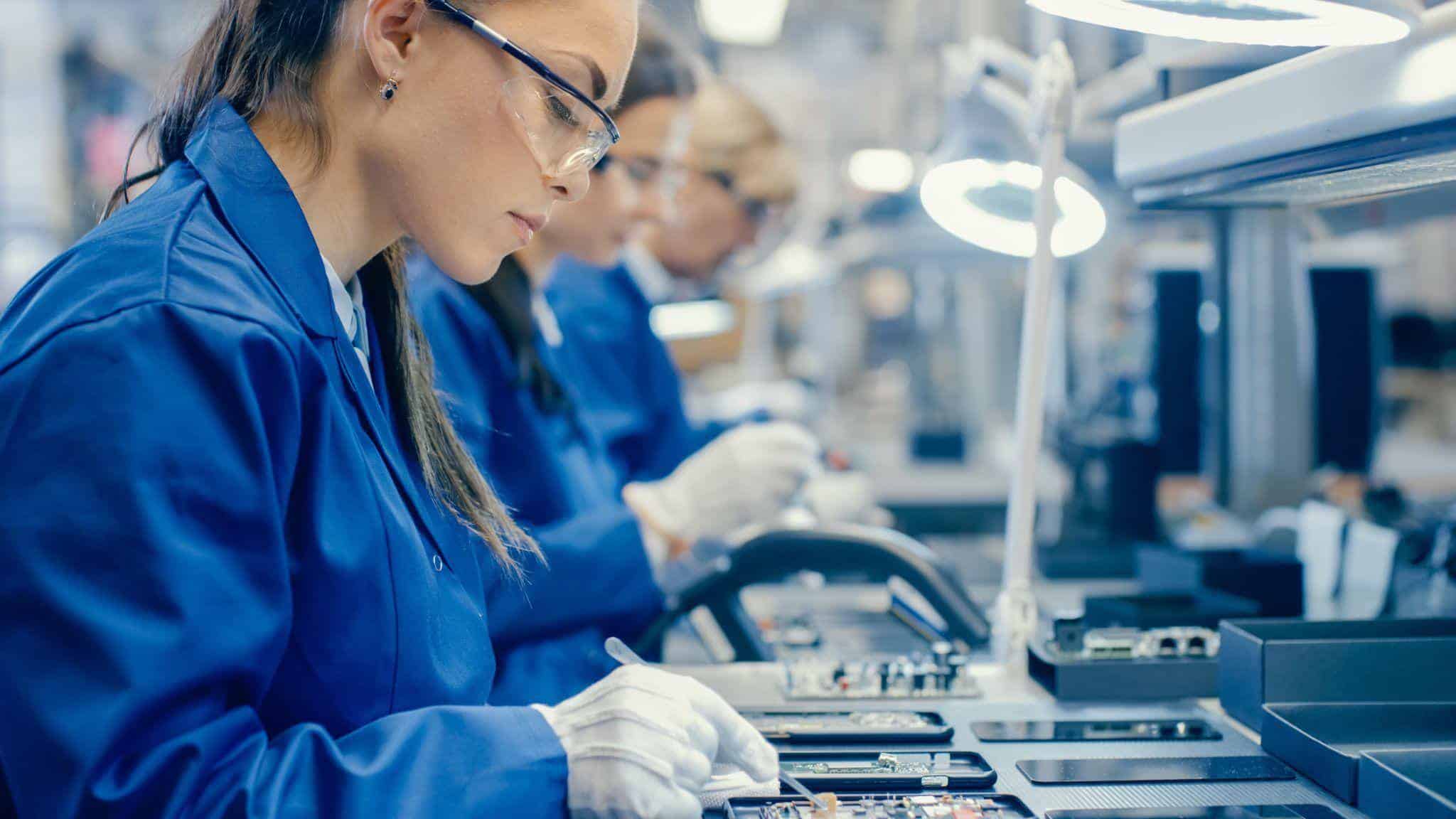
How we approach facility layout design
After establishing your size requirements, we design a specific building configuration and prepare a preliminary scope of work. Then, we identify all aspects of the manufacturing plan floor plan including lighting, floor loads, clearances, entrances, flow patterns, process gas requirements and environmental requirements unique to your operations. The goal is to create a factory layout plan.
Based upon the facility’s plans, space programming analysis and defined operational flexibility, Campbell Corporation develops a schematic concept design to properly define the project at hand.
Process Flow
Process flow optimization is an essential part of facility layout design that delineates all production and warehousing equipment. At Campbell Corporation, we use Lean manufacturing and operational flexibility principles to develop a high-level process flow map for each product family to outline future efficiencies.
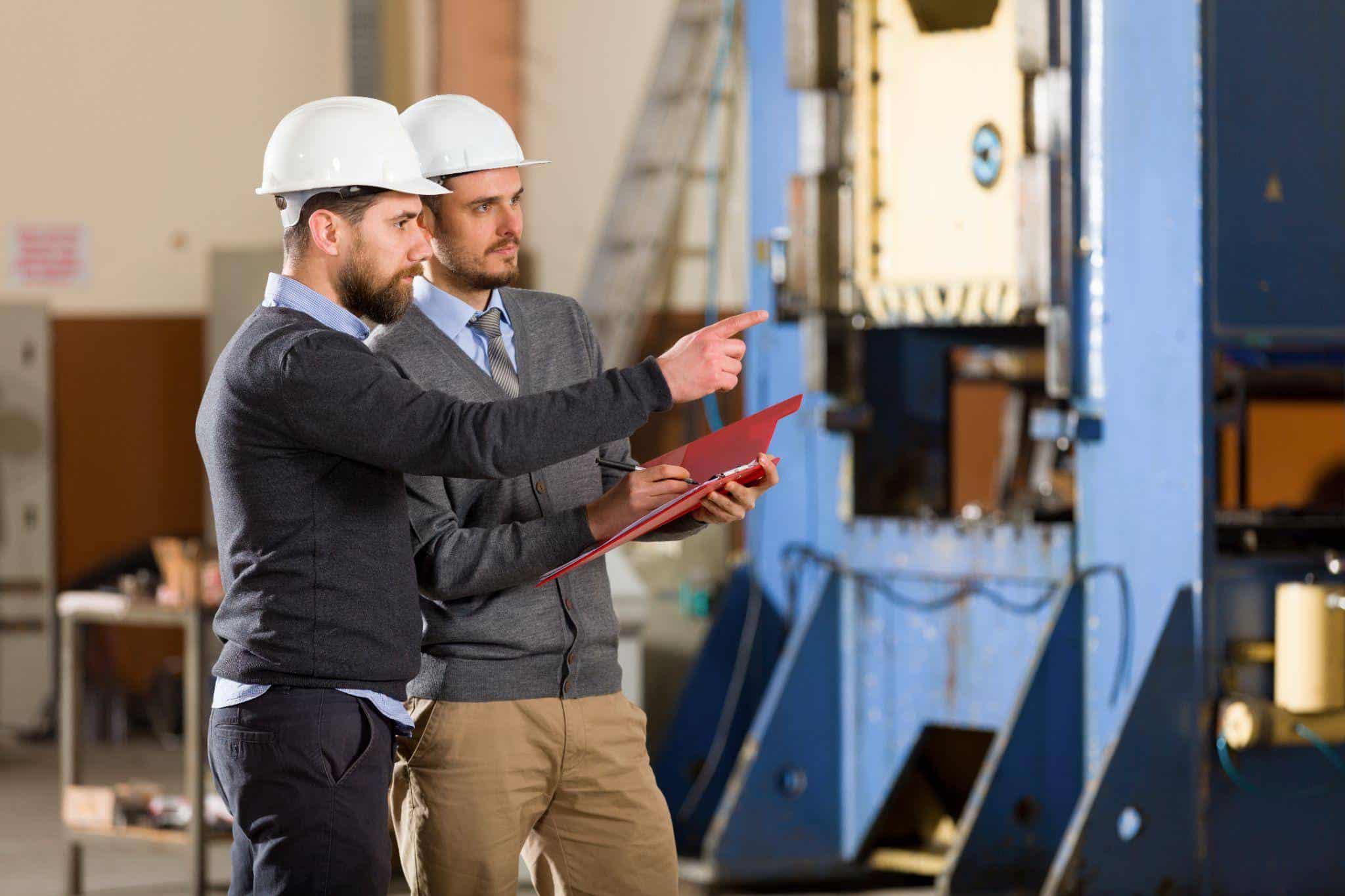
By understanding your future objectives, we can evaluate whether there is a cost reduction component, a capacity component, or a quality component. Then, we provide a factory layout design that will ensure you’ll be competitive and thrive within your industry.
Our methodologies include, but are not limited to:
- Value Stream Mapping
Flow chart which identifies value and non-value added activities within your operation. - Balanced Production
Improves productivity by providing optimal balance through various manufacturing areas. - Quick Changeover Management
Single Minute Exchange of Dies (SMED) principles to reduce changeover time. - Manufacturing Time Definition
Defining and planning production at the rate of your customers demand. - Line Capacity Analysis
Planning production line capacity to increase volume and On Time Delivery (OTD). - Production Control Systems (Andon)
System to notify management, maintenance, and other workers of a quality or process problem. This system provides an efficient and reliable production flow. - Single-Piece Flow and Work-in-Process Management
Eliminates waste through incremental improvement. - Reception and Warehouse Process Architecture
Data warehouse implementations to ensure improved inventory processes. - Constant Daily Output and Leveling Production
Provides systemically controlled productivity and a steady production flow to improve on-time delivery and efficiency. - Inventory Management and Kanban
Systems to control the logistics of the inventory. - Production and Logistic Equipment Layout
Depicts all production and warehousing equipment, which helps define building size and operational flexibility.
Our clients typically achieve at least:
More On-Time Deliveries
Better Inventory Turnover Performance
Increase in Productivity
Space Saved
Building Schematic Design
Building schematic design is based on the manufacturing goals and requirements of the facility, including comprehensive plans, designs, and specifications.
The manufacturing process and owner requirements are then transmitted to the design architect, structural engineer, HVAC engineer, electrical engineer, mechanical engineer, etc.
Campbell Corporation considers all design impacts, material handling requirements, raw materials, and WIP storage requirements, production equipment structural and mechanical requirements, code considerations, client branding, building components, and more.
Office and Support Area Design
Campbell Corporation conducts space planning principles and processes to integrate maximum efficiency and superior functionality. Our office area design work utilizes adjacency studies to promote effective collaboration in the workspace. With every facility layout and design project, our team of Lean engineers will develop a deep understanding of your goals in order to create a strategic plan for manufacturing cycle efficiency.
Campbell Corporation’s Lean manufacturing facility planners complete a thorough review of your company’s capabilities and limitations. We develop a value added, high-impact plan to elevate operations within your industry. With a complete understanding of your business and customer needs, along with your input, Campbell Corp will significantly raise your profit margin while your customers benefit from substantial productivity, functionality and an overall increase in quality.
Production and Logistic Equipment Layout
The production and logistic equipment layout depicts all production and warehousing equipment in addition to racking, which helps define building size, process flow and operational flexibility.
MAKE THE MOST OF YOUR IMPORTANT INVESTMENT
OTHER SERVICES

Lean Manufacturing Consulting
Have a facility already? You can still increase revenue with Lean techniques. Campbell Corporation’s seasoned experts get under the hood of your operation to make effective Lean manufacturing recommendations. You could benefit from immediate results including increased profitability and efficiency.